Our quality management
A systematic approach is the standard for every development. Our DIN EN ISO 13485-certified quality management system and our in-process controls give you peace of mind in every respect. Our cleanroom production is fully automated - from the injection molding cell to the automated guided vehicles (AGVs) and automated packaging systems. This provides even greater product protection and patient safety in the manufacture of plastic products for the pharmaceutical and medical device industries.
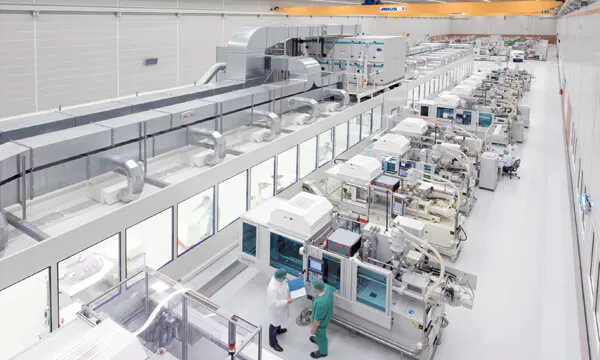
Monitoring
Regular monitoring of microbiology, airborne particle contamination, temperature, pressure, humidity, compressed air quality and air velocity is standard in our production facilities.
In addition to cleanroom production according to GMP Class C and ISO Class 7 of DIN EN ISO 14644-1, we have defined our own conditions for production outside this area. For this purpose, we have defined our own GMP Class E for microbiology based on ISO Class 9 of DIN EN ISO 14644-1.
Our facilities are equipped with air conditioning and ventilation systems. Class F7 intake filters are installed. The temperature is 24°C +/- 3°C. Constant temperature and air quality have a positive effect on microbiology.
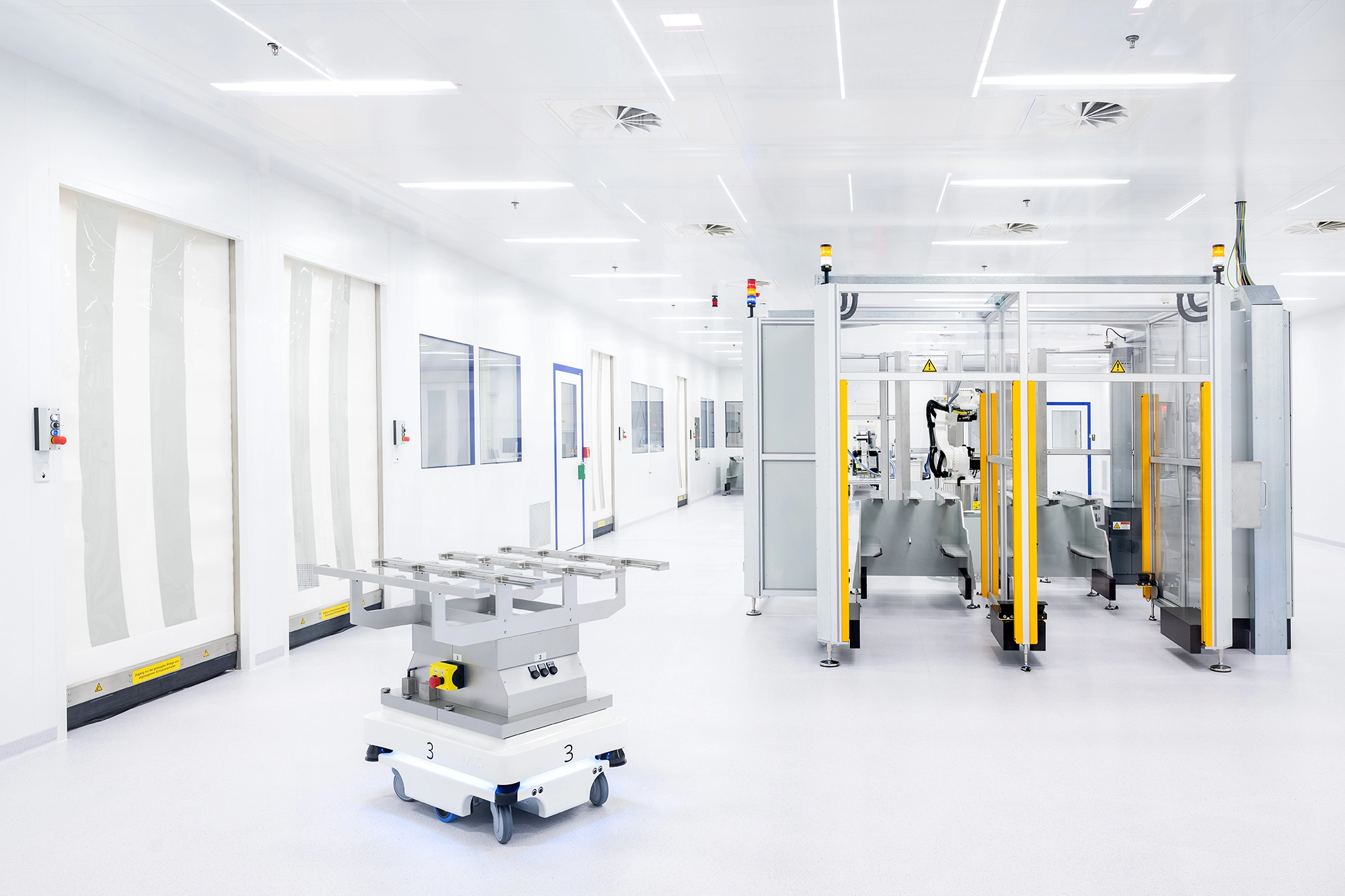
Production environment
Our cleanroom production is equipped with filter systems that guarantee a particle and germ content in accordance with DIN EN ISO 14644 - Class 7 and Class C of the EC GMP guidelines. That is less than 350,000 particles/m3 down to a size of 0.6 µm and less than 100 microorganisms/m3.
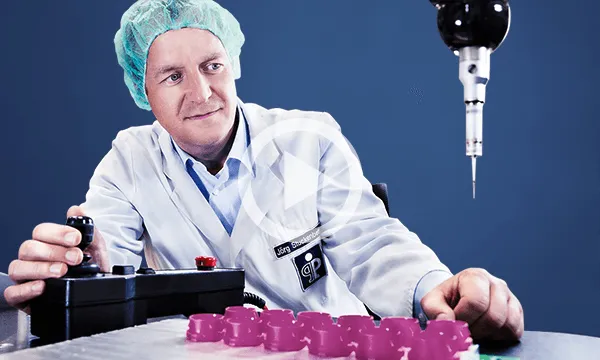
Quality assurance
Continuous measuring, testing and documentation is standard for us. Every item is tested to a hundredth of a millimeter in accordance with a certified quality management system. This means you can rely on consistently high product quality, especially in series production.
Awarded and certified.
Continuous quality assurance.
From the start of component development to the release of the mold design, the highest demands are placed on technology and quality. In four qualification steps, the manufacturing process is tested and documented in detail across all phases of industrialization.
Design Qualification (DQ)
The requirements for the component are specified in the specifications and implemented by selecting a suitable mold concept.
Installation Qualification (IQ)
After the mold has been completed, this step checks whether it has been created in accordance with the DQ specifications. At the same time, tests are coordinated with the customer.
Operational Qualification (OQ)
This phase is used to find a safe process window. The process parameters are determined and documented with a view to their effects on the component by means of „DOE tests“ („Design of Experiments“). As part of this „functional qualification“, both the performance capability of the mold and the machine capability are examined.
Performance Qualification (PQ)
In this qualification step, the process and its influencing parameters are known to the best of our knowledge. The process capability of the component is determined and assessed. On completion of the PQ, the component is released for series production.