Our production technologies
Plastic parts in the pharmaceutical and medical device industries are subject to stringent cleanliness and hygiene requirements. The focus is on maximum product protection and patient safety. From the start of component development through to series production, the highest demands are placed on technology and quality. We also focus on solutions that minimize greenhouse gas emissions. Consistent quality, high production output and exemplary cleanliness characterize our GMP Class E production. A modern machine park with clamping forces between 250 kN and 1,300 kN is the hallmark of reliable volume production.
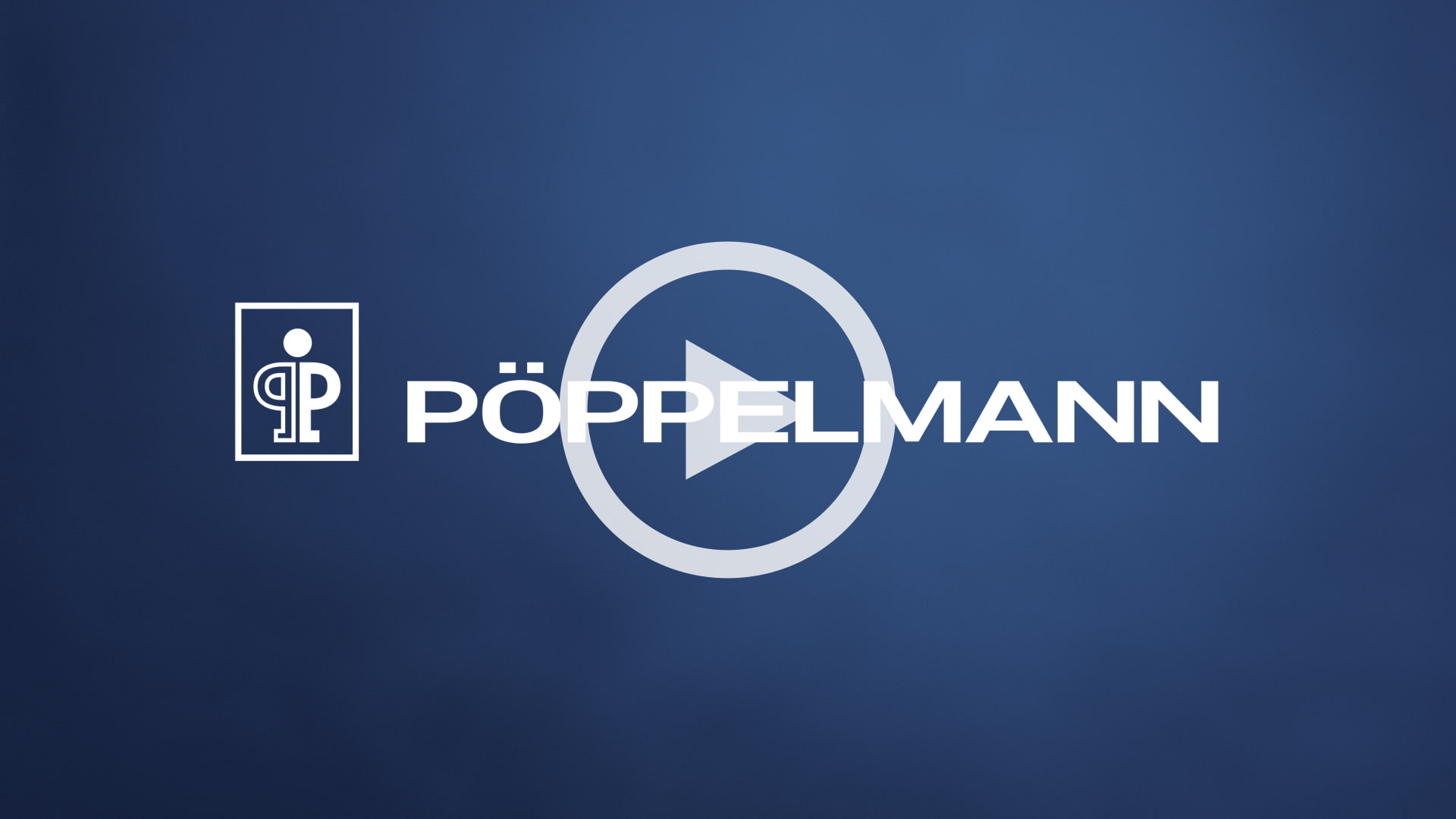
Injection molding
Functional parts
Multi-component injection molding
Integrated test stations
Injection molding is a process for the highly automated production of plastic items by processing granulate. We mainly use thermoplastics such as polypropylene (PP) or polyethylene (PE). Complex shapes with different surfaces can be produced in almost any size. The manufacturing process can be fully automated. Multi-component injection molding can also be used to produce sophisticated multifunctional parts. The raw material in granulate form is melted and injected into an injection mold under high pressure. After cooling, the article can then be ejected or removed using automation.
Your benefits at a glance:
- Consistent quality, high production output, exemplary cleanliness
- Use of different materials
- Also suitable for high component requirements
- Fully automated production process, in some cases with integrated test station
Material logistics
Underfloor supply
Central material supply
Double-chamber silo
We rely on high-tech series production in order to meet the high product requirements of our customers and implement them economically. Our production is characterized by a central underfloor supply of material, cooling water, compressed air, energy and air conditioning. In addition, our injection molding machines in production are supplied centrally and fully automatically with material from the double-chamber silos. The material flow can be programmed individually for each machine.
Your benefits at a glance:
- Consistent quality and high process reliability
- Fully automated processes and high production output
- Use of individual materials
- Batch tracking using double-chamber silos
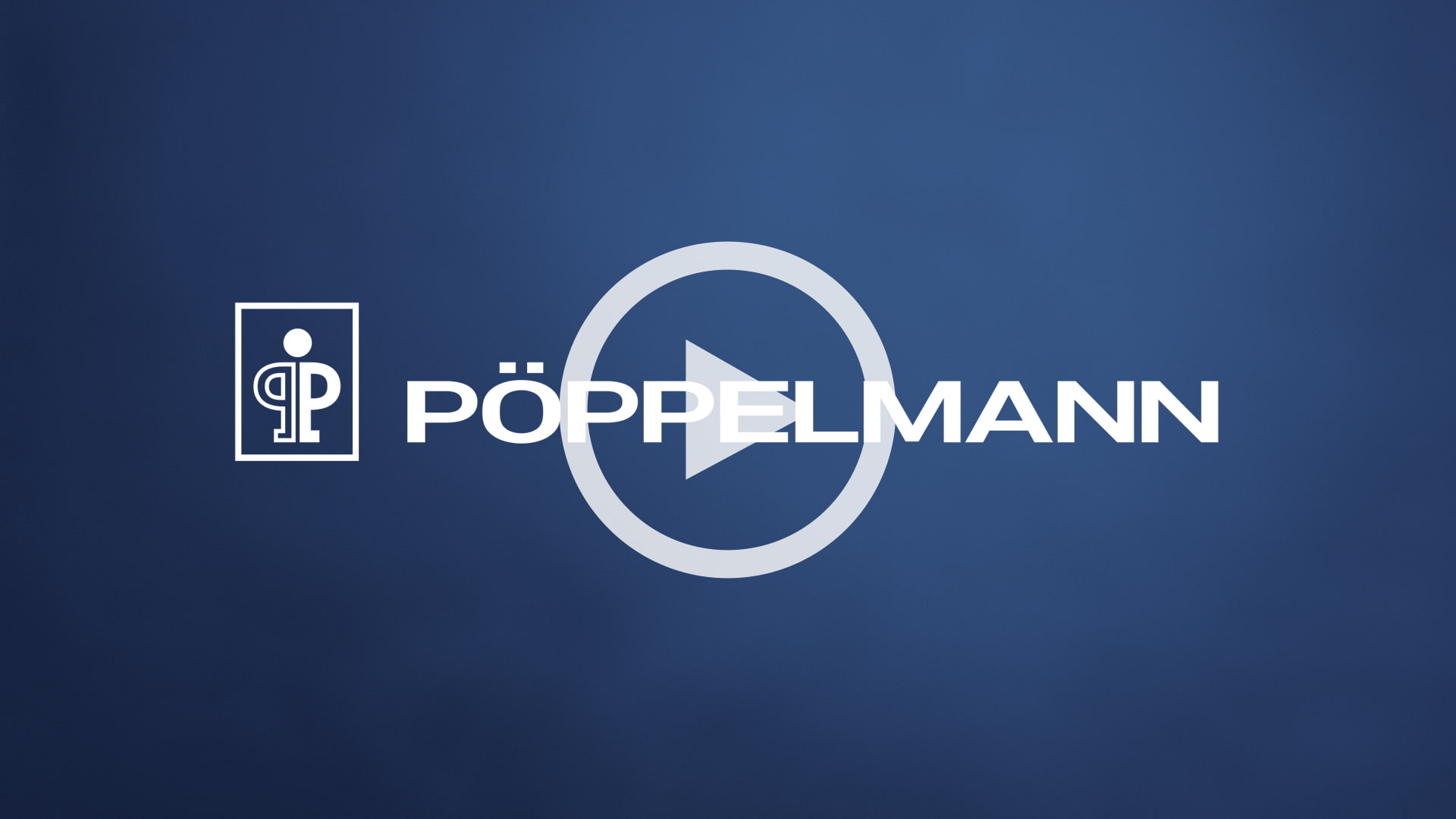
Cleanroom production
Lab & Diagnostics
Medical Devices
Pharma & Healthcare
Plastic parts and assemblies with the highest standards of cleanliness are manufactured under certified clean room conditions (DIN EN ISO Class 7, GMP Standard – C). The area of our injection molding cells in the cleanroom is supplied with clean air by a laminar flow module. This means that the injection molding machines, including the control cabinets, auxiliary equipment, etc., can be located outside the cleanroom. This reduces the heat load and power requirements of the air conditioning system. The mold area outside the cleanroom is easily accessible for mold changes and maintenance work without affecting the processes in the cleanroom and therefore the quality of the plastic parts. An accident on an injection molding machine or an auxiliary unit does not usually result in contamination of the cleanroom.
Your benefits at a glance:
- Less than 350,000 particles/m3 (down to a size of 0.6 μm)
- Autonomously operated cleanrooms with separate air conditioning and filter system
- Picking of individual parts and assemblies and assembly
- DIN EN ISO 14644 Class 7, GMP Standard – C
- Quality management system according to DIN EN ISO 13485
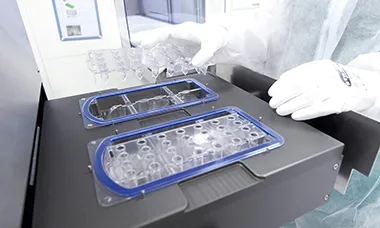
Assembly
Further processing
Packaging solutions
Fabrication techniques
Innovative and dynamic process and assembly technology has always been standard. For good reason, because optimized production processes help to effectively save costs - whether by means of fully automated assembly and packaging solutions or packaging solutions integrated into the production process. Depending on the application, the subsequent processes include fully automated assembly, efficient filling techniques, labelling and packaging. At the end of the process chain, the products are packaged in secondary packaging agreed with the customer. Versatile and tried-and-tested processes such as hot gas welding or vibration welding are standard here.
Your benefits at a glance:
- Effective cost savings through lean processes.
- Reduced component contamination through fully automated processes.
- Packaging in „sales packaging“.
- Assembly under clean room conditions.
- Fabrication technology - higher product quality, shorter cycle times.
Fully automated
cleanroom
cleanroom
Less particle sources, even more safety.
From the injection molding cell to automated guided vehicles (AGVs) and automated packaging systems, the new fully automated cleanroom production system generates fewer particle sources. As a result, we can offer even greater product protection and maximum patient safety in the manufacture of plastic products for the pharmaceutical and medical device industries.
Thinking ahead
together.
together.
The responsible use of natural resources to protect the environment and the climate is a matter of course for many companies today. However, in areas such as medical technology and pharmaceuticals, regulatory requirements make it more difficult to implement. The focus is on application safety with maximum product protection. Nevertheless, we develop customized solutions that take into account the sustainable use of resources.
Material
We reduce the use of materials through resource-saving article concepts and efficient production processes.
Greenhouse gas emissions
The use of recycled materials, high recyclability and environmentally friendly production conditions can maximize GHG reductions.
Logistics & process
By optimizing the design of the item, stacking and nesting can be improved - maximizing the quantity per package unit and minimizing setup time on the production floor.
Storage &
Energy
Optimized nesting allows for optimal use of existing capacity. The space required for internal and external logistics is reduced, resulting in cost savings.