THERMOFORMING WITH IN-MOULD-LABELLING. THE LIGHTEST PACKAGING DESIGN WITH IML.
Until now, In-Mould-Labelling technology has only been used for plastic injection-molded packaging. With the realization of a thermoformed dairy cup with IML, we combine our many years of experience in the areas of IML and thermoforming. The innovative and efficient T-IML process makes it possible to produce cups that are very light, as less plastic is used, and at the same time have a high-quality decoration.
Your benefits at a glance:
High-quality decoration thanks to In-Mould-Labelling
IML is a captive component of the packaging - moisture and temperature resistant and dishwasher safe.
Maximum material savings through the use of thermoforming technology
Compared to injection molding, less plastic is used in thermoforming. Cups are significantly lighter (savings of 25% are no exception).
Maximum recyclability, as monomaterial packaging
Maximum recyclability: cup and In-Mould-Label are made of the same material (polypropylene). This means that the cups are very easy to recycle as monomaterial packaging.
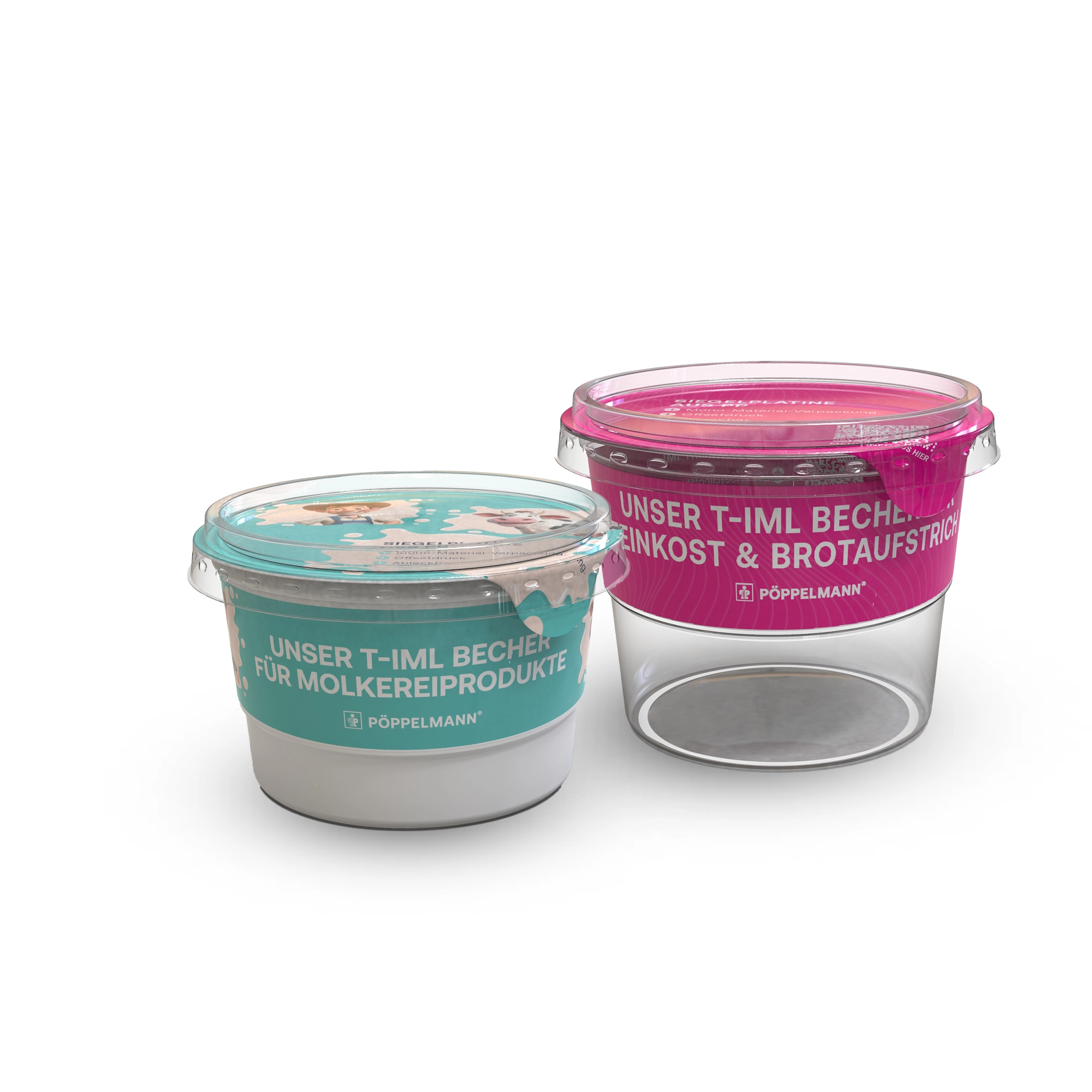
BDT series | thermoforming cups with In-Mould Labelling in detail.
Our T-IML tubs are available in various sizes - so the right tubs are available for many applications in the dairy or delicatessen sector.
Thermoforming with IML: minimum material usage, maximum recyclability.
With In-Mould-Labelling (IML), plastic packaging is provided with a pre-printed plastic label during production. To do this, a robot positions the printed, thin plastic film in the mold. After the production process, the label and molded part form an inseparable unit with a continuous surface. This decoration process is therefore the ideal basis for mono-material packaging. Due to the same base material for label and plastic article, IML-decorated articles are optimally recyclable.
Material
We reduce the use of materials through resource-saving article concepts and efficient production processes.
Greenhouse gas emissions
The use of recycled materials, high recyclability and environmentally friendly production conditions can maximize GHG reductions.
Logistics &
process
By optimizing the design of the item, stacking and nesting can be improved - maximizing the quantity per package unit and minimizing setup time on the production floor.
Storage &
Energy
Optimized nesting allows for optimal use of existing capacity. The space required for internal and external logistics is reduced, resulting in cost savings.
What do we mean by
future-proof packaging?
future-proof packaging?
The EU Packaging & Packaging Waste Regulation (PPWR) sets out the framework conditions for how packaging should be designed in the future. Unnecessary packaging and packaging waste should be reduced and reusable systems and recycling should be promoted. In our opinion, plastic packaging meets precisely these requirements, as plastic is more efficient than alternative materials.
Mainly less plastic?
Plastic is more efficient than alternative materials.
On the
The wrong track?
PPWR is driving deforestation and the growth of waste mountains.
Minimum recyclate usage?
100% in unregulated sectors (e.g. nonfood) creates incentives for investment in mechanical recycling.
Design For
Recycling?
Recyclability and the use of recyclates are the basis for a functioning circular economy.