Unser Qualitäts-
management
management
Eine systematische Herangehensweise ist der Standard für jede Entwicklung. Unser nach DIN EN ISO 13485 zertifiziertes Qualitätsmanagement und unsere In-Prozess-Kontrollen bieten Ihnen Sicherheit in jeder Hinsicht. Unsere Reinraumproduktion ist vollautomatisiert - von der Spritzgießzelle über fahrerlose Transportsysteme (FTS) bis zur automatisierten Verpackungsanlage. Das bietet noch mehr Produktschutz und Patientensicherheit bei der Herstellung von Kunststoffprodukten für die Pharmaindustrie und Medizintechnik.
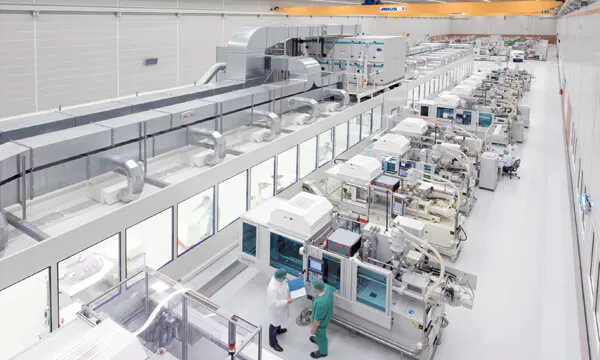
Monitoring
Ein regelmäßiges Monitoring von Mikrobiologie, Partikelbelastung der Luft, Temperatur, Druck, Luftfeuchtigkeit, Druckluftqualität und Luftgeschwindigkeit ist in unseren Produktionshallen Standard.
Neben der Reinraumproduktion nach der GMP-Klasse C und der ISO-Klasse 7 der DIN EN ISO 14644-1 haben wir für die Produktion außerhalb dieses Bereiches eigene Bedingungen festgelegt. Hierzu haben wir eine eigene GMP-Klasse E für die Mikrobiologie in Anlehnung an die ISO-Klasse 9 der DIN EN ISO 14644-1 definiert.
Unsere Hallen sind mit einer Klima- und Lüftungsanlage ausgestattet. Es sind Ansaugfilter der Klasse F7 verbaut. Die Temperatur beträgt 24°C +/- 3°C. Gleichbleibende Temperaturen sowie die Luftqualität wirken sich positiv auf die Mikrobiologie aus.
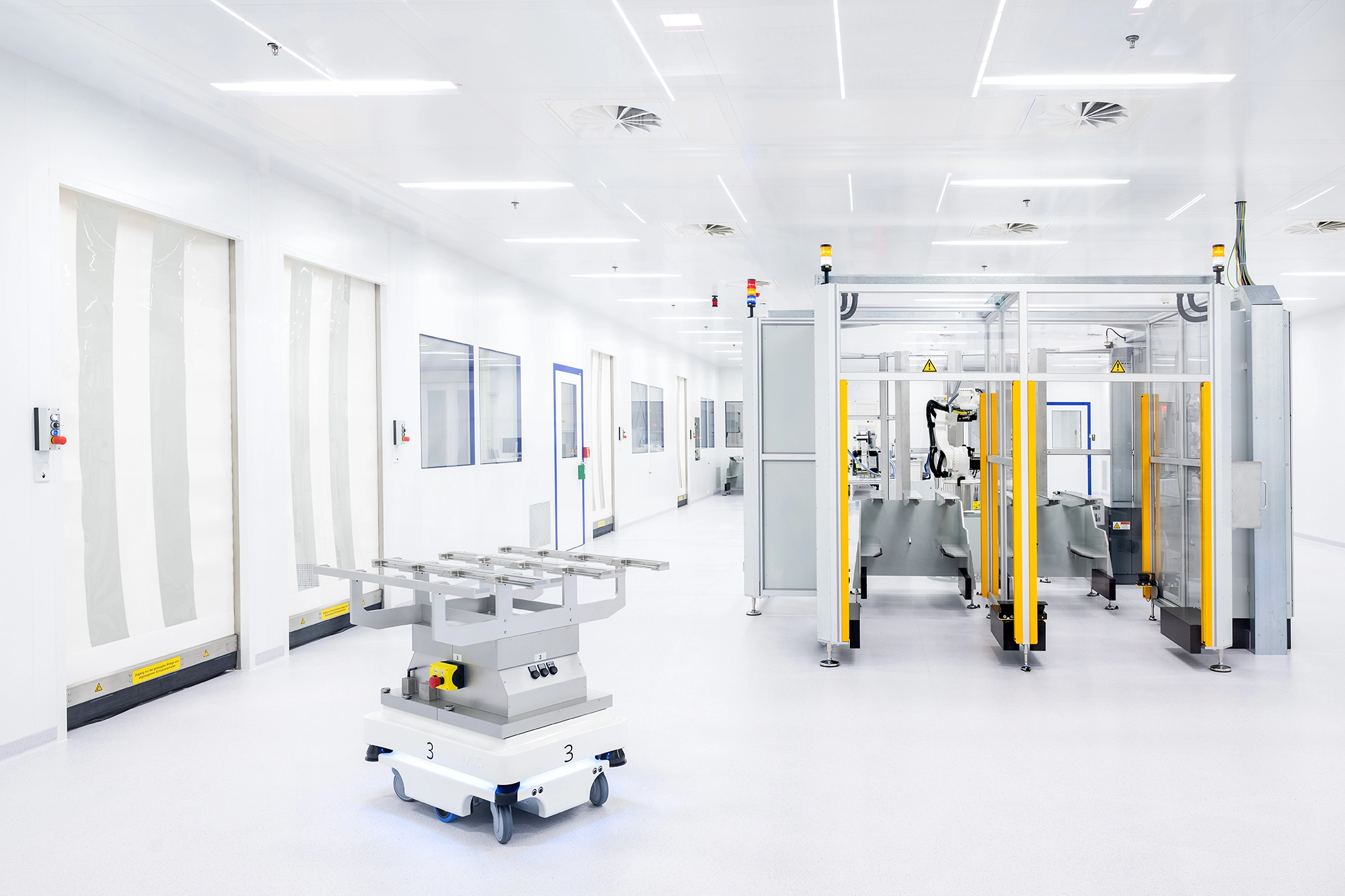
Produktionsumgebung
Unsere Reinraumproduktion ist mit Filteranlagen ausgestattet, die einen Partikel- und Keimanteil gemäß DIN EN ISO 14644 - Klasse 7 und Klasse C des EG-GMP-Leitfadens gewährleisten. Das sind weniger als 350.000 Partikel/m3 bis herab zu einer Größe von 0,6 µm und weniger als 100 Keimbilder/m3.
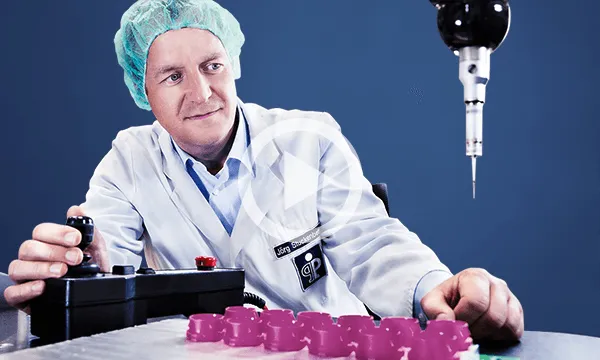
Qualitätssicherung
Kontinuierliches Messen, Prüfen und Dokumentieren ist für uns Standard. Jeder Artikel wird nach zertifiziertem Qualitätsmanagementsystem bis auf Hundertstel Millimeter genau geprüft. So können Sie sich gerade bei der Serienproduktion auf eine konstant hohe Produktqualität verlassen.
Ausgezeichnet und zertifiziert.
Kontinuierliche Qualitätssicherung.
Vom Start der Bauteilentwicklung bis zur Freigabe der Werkzeugkonstruktion werden höchste Anforderungen an die Technik und Qualität gestellt. In vier Qualifizierungsschritten wird der Fertigungsprozess bis ins Detail über alle Phasen der Industrialisierung geprüft und dokumentiert.
Design Qualification (DQ)
Die Anforderungen an das Bauteil werden im Lastenheft spezifiziert und durch die Auswahl eines geeigneten Werkzeugkonzepts umgesetzt.
Installation Qualification (IQ)
Nach der Fertigstellung des Werkzeuges wird in diesem Schritt überprüft, ob dieses gemäß den Vorgaben der DQ erstellt worden ist. Parallel werden Prüfpläne mit dem Kunden abgestimmt.
Operational Qualification (OQ)
Diese Phase dient der Findung eines sicheren Prozessfensters. Die Prozessparameter werden mit Blick auf ihre Auswirkungen auf das Bauteil durch „DOE-Versuche“ („Design of Experiments“) ermittelt und dokumentiert. Im Rahmen dieser „Funktionsqualifizierung“ wird sowohl die Leistungsfähigkeit des Werkzeuges, als auch die Maschinenfähigkeit untersucht.
Performance Qualification (PQ)
In diesem Qualifizierungsschritt ist der Prozess mit seinen Einflussparametern bestmöglich bekannt. Die Prozessfähigkeit des Bauteils wird ermittelt und beurteilt. Mit Abschluss der PQ erfolgt die Freigabe für die Serienproduktion.
Diese Themen könnten Sie auch interessieren:
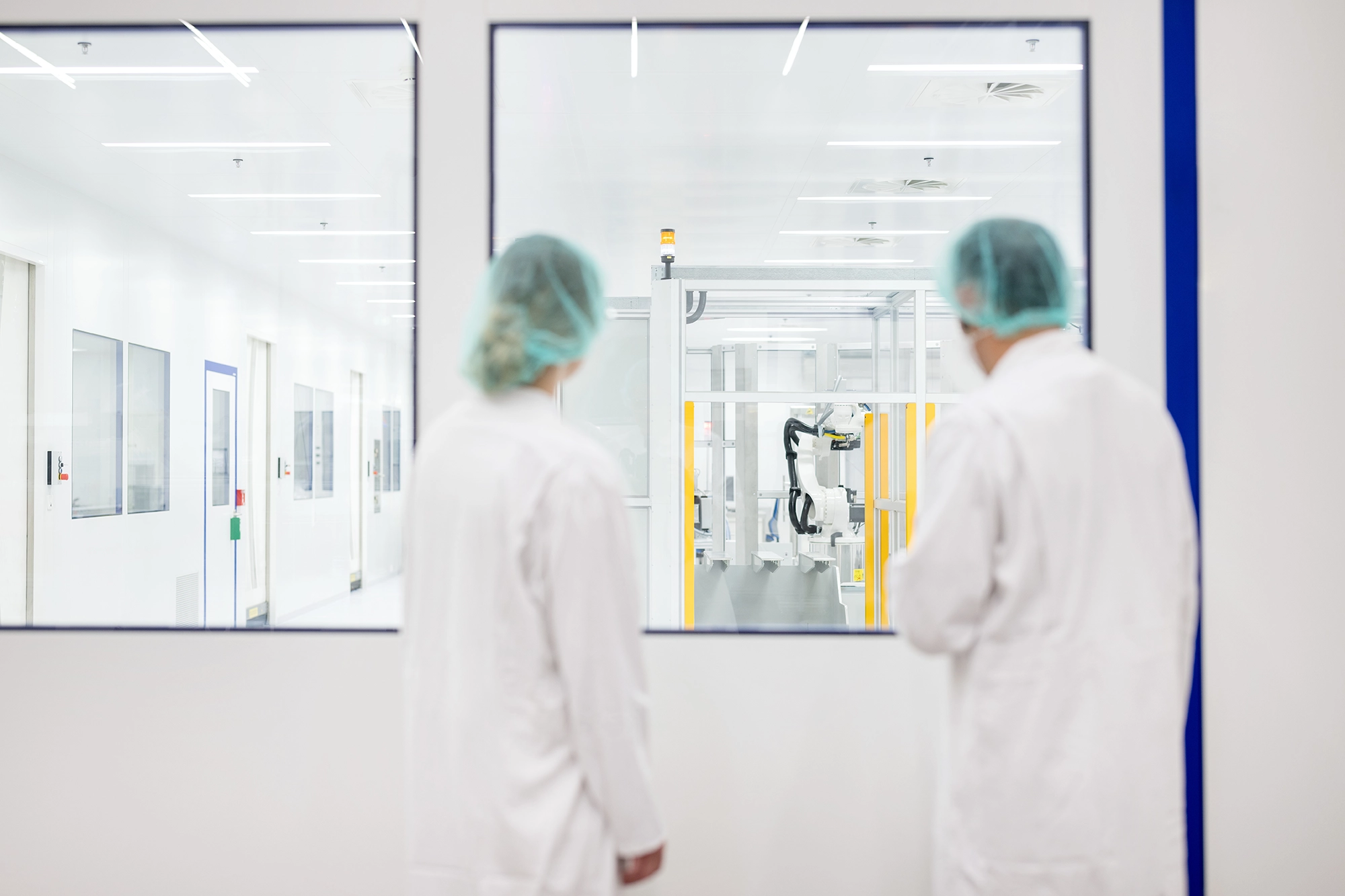
Reinraum
Zertifiziert nach DIN EN ISO Klasse 7, GMP Standard C.

Produktion
Einzelteilfertigung und Montage mehrteiliger Baugruppen.
Produkt-
entwicklung
Individuelle Bauteile und Baugruppen.