„The collaboration with Pöppelmann has intensified in recent years in particular, which has also led to both companies developing an understanding of each other's requirements. One of the results of this good cooperation is our new herb quark cup, on which numerous departments at DMK and Pöppelmann have worked together.
Henning Götsche, Packaging Development of the DMK Group's Private Label business unit
Small cup, big impact:
a project to conserve resources.
a project to conserve resources.
Less material usage, lower weight, optimized logistics: the reworking of a private label tub for herbal quark proves that even established packaging solutions offer potential for optimization. With the redesign of the cup, a joint project between the DMK Group and the packaging manufacturer Pöppelmann FAMAC®, significant resource savings can now be achieved, contributing to greater climate protection.
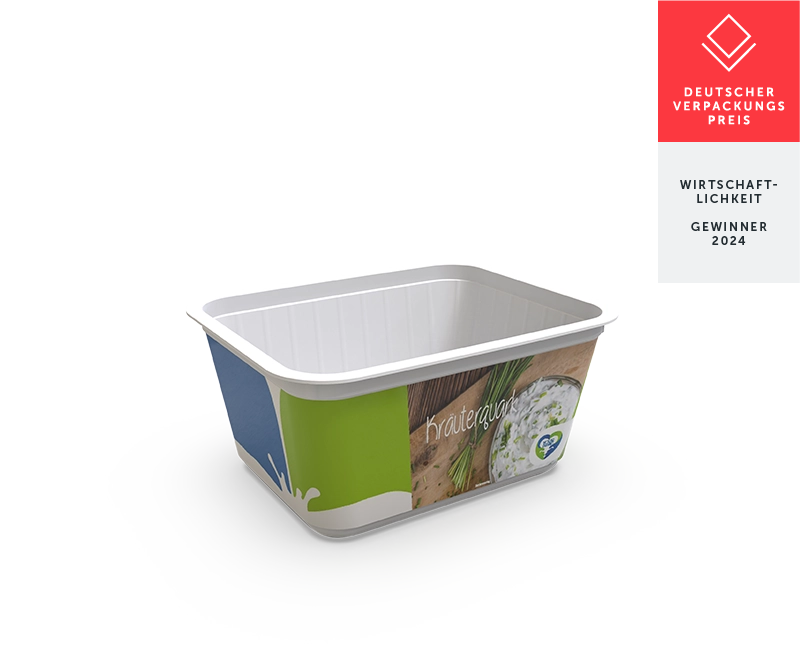
Two companies, one common goal - more resource conservation
The joint project proves that there is certainly room for optimization even with long-standing, established packaging solutions such as the classic quark pot. DMK took the first step some time ago by dispensing with the conventional snap-on lids on tubs for selected quark products. This has already saved considerable amounts of plastic. In a recent project, the dairy products manufacturer went one step further. The aim was to also optimize the injection-moulded cup in terms of material usage in order to save even more plastic.
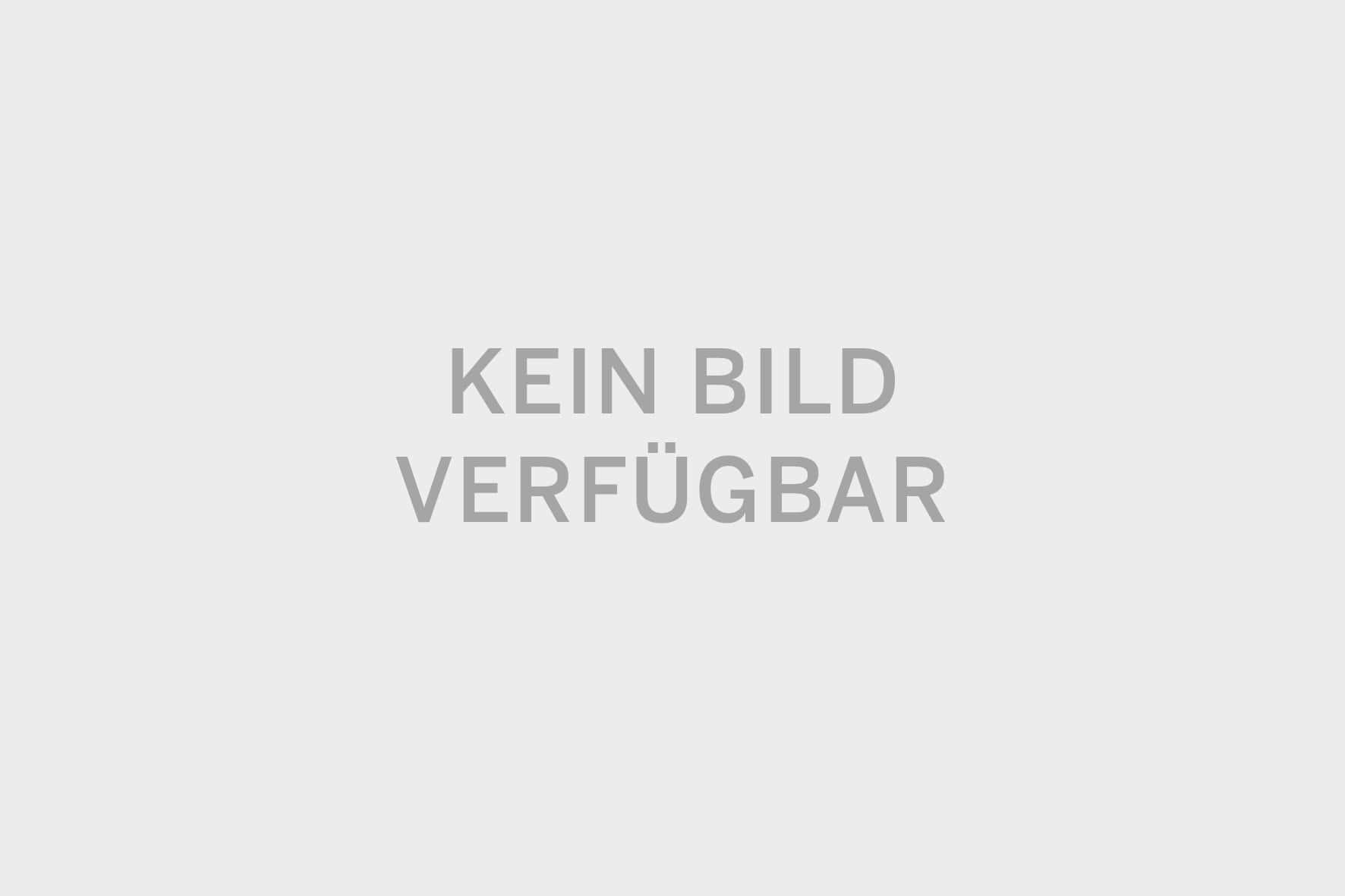
reudce COSTS AND GREENHOUSE GAS EMISSIONS WITH AN INNOVATIVE PACKAGING DESIGN.
20% less weight
Weight saving thanks to increased length of ribs: the reduction in material reduced around 20 percent in GHG emissions: (18.4 instead of 23.09 kg CO2eq/1,000 cups)
Recycling capability
In the In-Mould-Labelling process, the container is provided with a pre-printed plastic label during production.The container and label are made from the same base material, making it easy to recycle the packaging.
Nesting
Adapting the design of the cup made it possible to reduce the stacking distance and cup height. This reduces the storage space required and the number of transports from the packaging manufacturer to the filler. Instead of 8,736 cups, 13,440 now fit into one transport box. This reduces the annual need for transport packaging for the unfilled cups by around 50 percent. It also leads to improvements in the filling process (50% more cups in the magazine reduce the workload in production).
There are numerous potential savings along the value chain. We would be happy to present these to you in a personal meeting:
Reduce
Thanks to material reductions and optimal stackability and nestability
recycle
Recyclable through monomaterial
MARCO VON DÖLLEN
sales MANAGER
What do we mean by
future-proof packaging?
future-proof packaging?
The EU Packaging & Packaging Waste Regulation (PPWR) sets out the framework conditions for how packaging should be designed in the future. Unnecessary packaging and packaging waste should be reduced and reusable systems and recycling should be promoted. In our opinion, plastic packaging meets precisely these requirements, as plastic is more efficient than alternative materials.
Mainly less plastic?
Plastic is more efficient than alternative materials.
On the
The wrong track?
PPWR is driving deforestation and the growth of mountains of waste.
Minimum recyclate usage?
100% in unregulated sectors (e.g. nonfood) creates incentives for investment in mechanical recycling.
Design For
Recycling?
Recyclability and the use of recyclates are the basis for a functioning circular economy.
Test without obligation: reusable cups from the FAMAC® program.
Request samples of our packaging for testing - of course, completely free of charge and without obligation.
Fill out the form now and receive a sample range.