Thermoform trays
Workpiece carriers, also known as trays or blisters, are used for the optimum handling of components, for example in the electronics, sensor or automotive sectors, during transportation, storage and production. Thanks to our in-house film production, we are very flexible and can respond specifically to your requirements. We can provide you with a quotation and development concept for your plastic workpiece carrier within a very short time. We can also produce a prototype of your product with the help of rapid manufacturing. As a specialist in protective solutions, we have a wide range of protective plugs and protective caps in addition to workpiece carriers. This enables us to offer all product protection solutions from a single source by means of optimum machine and tool concepts.
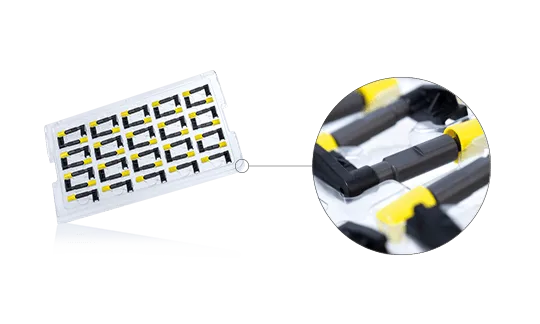
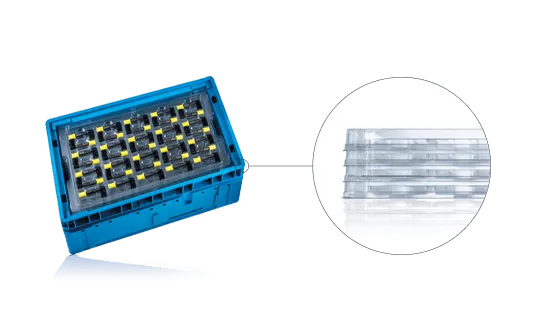
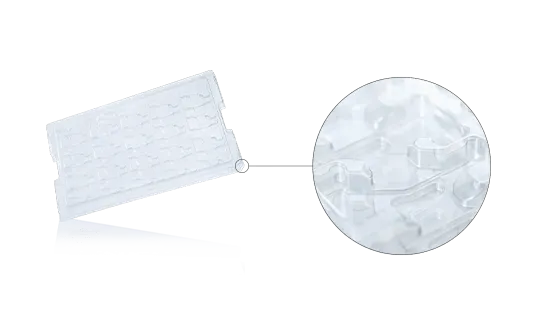
Workpiece carriers and trays for transportation.
We have been using the thermoforming process for over 40 years. We serve customers from a wide range of industries, including the automotive sector. If your workpiece carriers need to meet particularly high quality requirements, such as ESD protection, we can implement these for you. Our DIN ISO 9001:2015-certified quality system in combination with our own laboratory gives you the assurance that we comply with the agreed specifications in a reliable process.
The workpiece carriers for transport systems can be manufactured from various plastics. Common materials for the production of workpiece carriers are PET and PS. Our PS is obtained 100% from sustainable material streams as post-consumer recycled material. After the thermoforming trays have been used, the material can be recycled again, regardless of whether it was previously used once (disposable) or several times (reusable). You can find out more about the closed material cycle via our company-wide PÖPPELMANN blue® initiative here.
Variety of materials and colors of our workpiece carriers:
Many advantages for your complete protection.
Benefit from the many advantages of Pöppelmann KAPSTO®: Together we ensure that you are successful every day. Our competent project teams with 40 years of experience in the thermoforming process ensure that your products are protected in the best possible way - from the optimum use of materials to the optimum volume utilization of the components in the tray.
Fast, targeted and safe:
Pöppelmann KAPSTO® as your development partner.
- Everything from a single source: from the idea to series production.
- Quotation and development concept within one day.
- Rapid prototyping using printed trays.
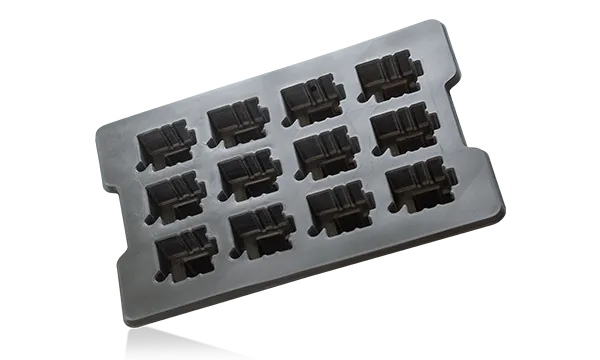
Exactly according to your wishes:
With Pöppelmann KAPSTO® to the solution for your application.
- In-house film production.
- Color and material selection according to customer requirements.
- Optional ESD protection possible.
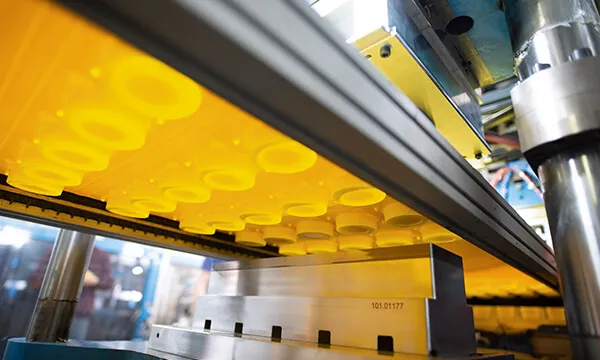
Closed material cycle:
Trays made from recycled plastic.
- Use of recycled materials on request.
- In-house recycling options.
- Your specialist for closed material cycles via the company-wide PÖPPELMANN blue® initiative.
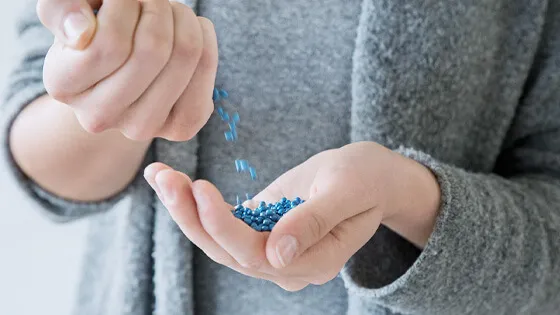
Tested and certified quality: from development to series production.
- Technical cleanliness on request.
- Certification in accordance with DIN ISO 9001:2015.
- Highest quality standards also for customers with particularly high requirements (e.g. from the automotive or electrical industry).
FREE SAMPLES
Did you know how well caps and plugs and thermoformed trays fit together?
Protective caps and plugs from our KAPSTO® standard range also provide optimal protection for your product. In some applications, they are used in combination with trays. We deliver all solutions around your product protection from one source. Request samples for testing and selection of possibilities – of course without obligation and free of charge.